Likely the foremost excellent, delicate and lustrous material ever created.
Silk dates back thousands of a long time and is still prized today as one of the most valuable and lavish fabrics. After all these a long time, the strategies of silk generation have changed very little.
Although the innovation of production strategies has advanced, silk production is still a labor-intensive handle that includes a parcel of difficult work.
What is silk made of?
A wide assortment of insects are as of now utilized to produce silk, but the most commonly utilized species are the hatchlings of the “bombyx mori”.
These unimaginable silkworms deliver one of the foremost looked for after materials with so numerous awesome properties.
Silk is shiny and lightweight, however extremely solid, and a single fiber of silk is stronger than an identical fiber of steel.
How is silk made?
Here, we walk you through the fascinating process by which silk is produced…
1.Sericulture:
It is a term referring to the process of collecting silkworms, harvesting cocoons, and gathering materials.
Female silk moths lay about 300 to 500 eggs at a time. These eggs eventually hatch to form silkworms, which hatch into larvae (caterpillars) in a controlled environment.
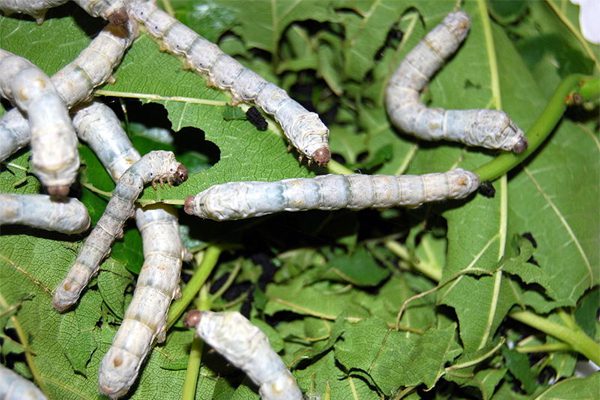
Silkworms continue to eat large amounts of mulberry leaves to encourage their growth. It takes about 6 weeks to reach full potential (about 3 inches). At this point, they stop eating and start raising their heads – that’s when the cocoon is ready to spin.
Attached to a fixed frame or tree, the silkworm begins spinning its silk cocoon by rotating its body in a figure-eight pattern about 300,000 times. This process takes approximately 3-8 days. Each silkworm produces only one silk thread about 100 meters long, bound by a type of natural rubber called sericin.
2.Thread removal
Once the silkworm has spun the cocoon, it is at last time to wrap yourself within the cocoon and take out the silk thread.
Place the cocoons in bubbling water to mellow and break down the elastic that holds the cocoons together. .
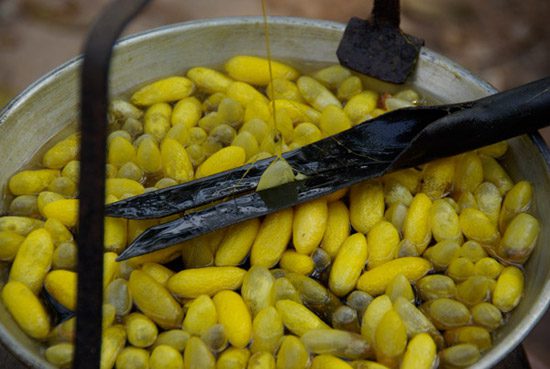
Each thread is then carefully reeled from the cocoon into individual long threads and wound onto a reel. Sericin may remain in the thread to protect the fiber during processing, but is usually washed off with soap and hot water.
3.Dyeing
After washing and scouring, the silk thread is bleached and dried before entering the dyeing process.
Traditional silk dyeing techniques use dyes from natural sources in the surrounding environment, such as fruit and indigo leaves.
A bundle of thread is soaked in a pot containing hot indigo leaves and water. This process is repeated many times over several days to ensure the right shade and quality.
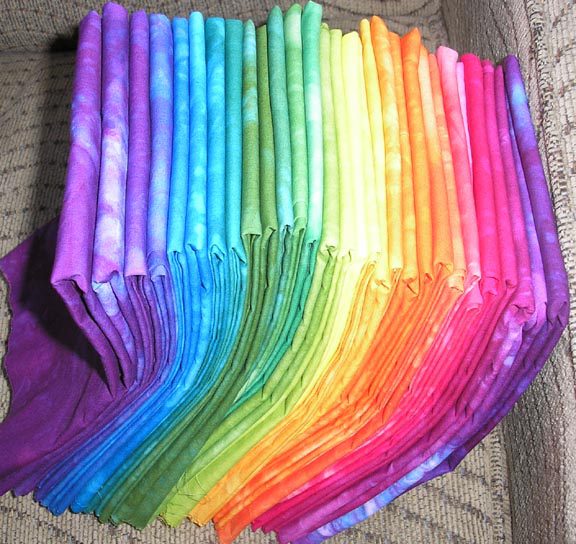
However, these traditional dyeing methods have all but disappeared in the commercial production of silk. Due to technological advances, manufacturers are choosing to use a variety of dyes instead, such as acid dyes and reactive dyes.This provides more color and shade options to meet a wider range of demands. .
That said, the general idea behind the technique is the same in that the silk is dipped in a dye bath to absorb the color. The silk is either fed into the bath via two cylinders or fixed to a round fixture that is immersed in the bath.
Manufacturers often prefer piece dyeing to reduce waste, so this will be one of the last steps in the process. By keeping solid white inventory ready for dyeing, we avoid having to overstock certain colors that are not ordered and may go unused.
Here at Biddle Sawyer Silks, we keep large quantities of silks in a wide variety of colors for immediate service with next-day delivery of silks we already have in stock.We also offer our own bespoke color palettes and wrap We also work with clients who can match samples via dip.
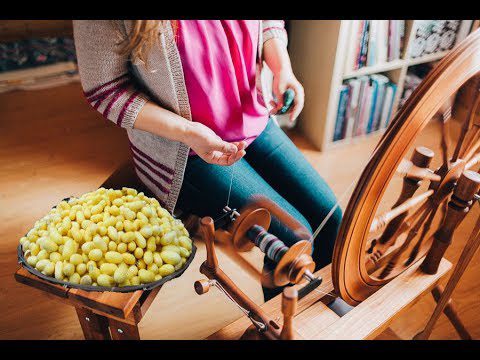
4.spinning
The traditional spinning wheel has been and will always be an integral part of the silk production process.Modern industrial processes have made it possible to spin silk yarn much faster, but it is simply a classic spinning wheel. It just mimics the functionality of .
The process of spinning basically unwinds the dyed fibers onto bobbins and flattens them ready for the weaving process. This can be done in a number of ways, from hand spinning to ring spinning to mule spinning.
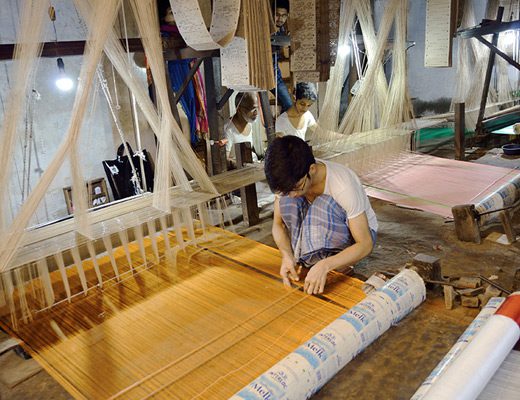
5.Weaving
Weaving is the method of putting together the final pieces of silk. There are numerous diverse ways to weave silk. Glossy silk weave, plain weave, and open weave are the foremost common, and silk wraps up shift depending on the weave.
Generally, weaving includes interlap two sets of strings that interweave with each other to make a solid, uniform texture. The strings are woven at right points to each other and the two distinctive points are called twist and weft. The twist strings run up and down the texture and the weft strings cross the texture.
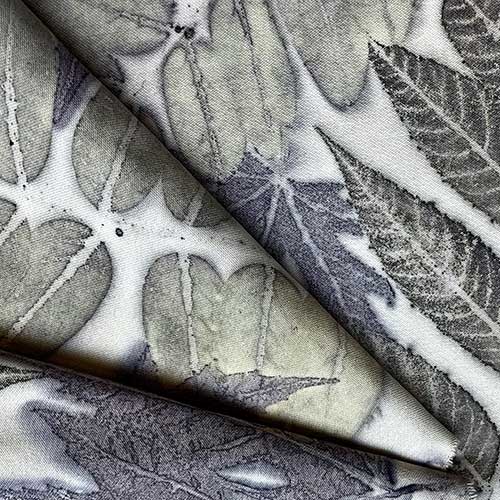
6.Printing
If you need a special pattern or design on the silk, it should be printed after pretreatment.This can be done in two ways: digital printing or screen printing.
Digital silk printing uses a specially designed textile printer to transfer hand drawn or digitally created artwork onto fabric using ink.
Screen-printing is a traditional, more hands-on method of creating essentially the same result, but in some cases, a thicker application of ink can result in a bolder, more vibrant look.
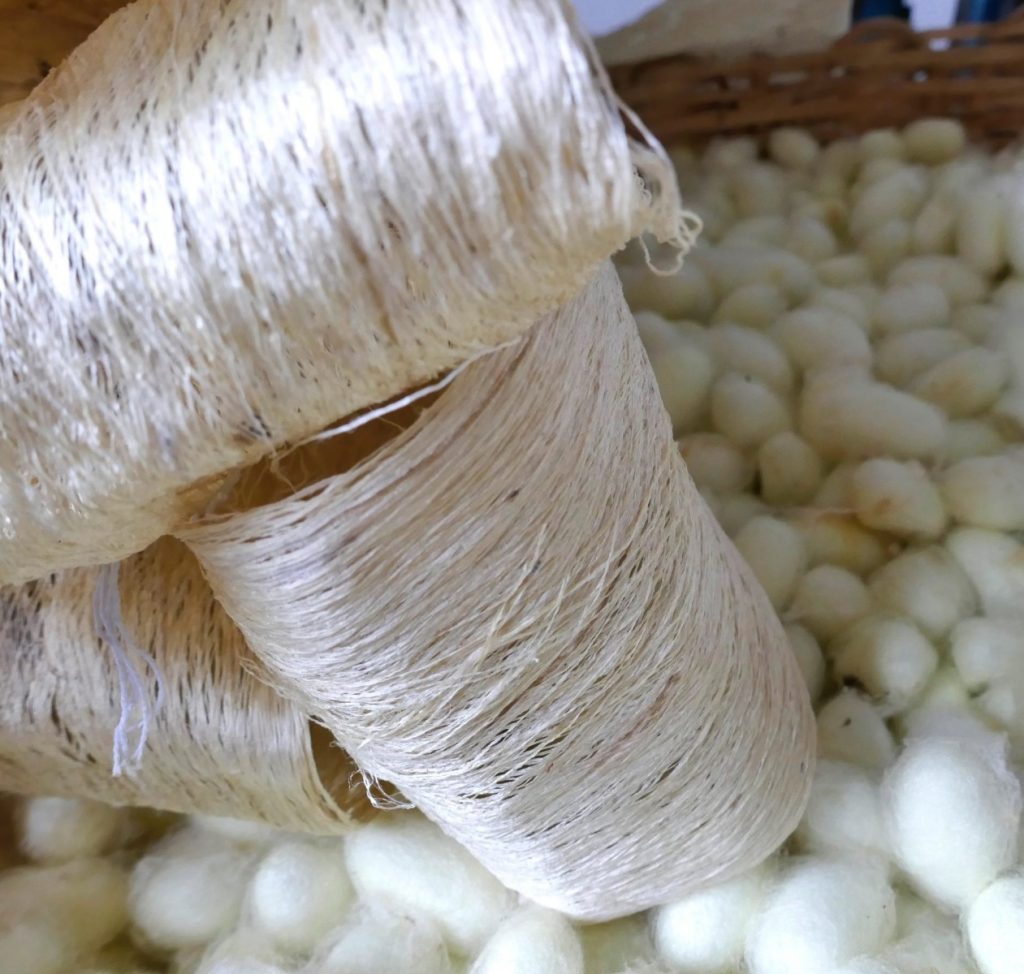
7.Finish
Silk must be finished to be considered ready for use. Finishing the silk gives it a very lustrous sheen that it is commonly known for, which is why it can achieve the desired look and feel.
Mainly by applying various chemical treatments many valuable properties such as fire resistance and wrinkle resistance can be added.